The production of laminated insulation material is a critical process for meeting industry standards and regulations. Every step of the way, from the selection of materials to the application of finishes, must be carefully planned and executed in order to create a product that meets all requirements.
This article looks at how manufacturers can ensure their processes meet both technical specifications and regulatory guidelines – from sourcing materials to maintaining quality control throughout the entire production cycle.
We will explore some key points that should be considered when producing this type of material, as well as providing an overview on how best practices are implemented by experienced suppliers in this field. With proper planning and execution, manufacturers can create products that not only meet industry standards but also deliver superior performance results.
Meeting Industry Standards and Regulations
When it comes to producing laminated insulation material, achieving industry standards and regulations is essential for ensuring a safe and effective product. To ensure these requirements are met, companies must take extra measures in the production process such as using high-grade materials when constructing their products.
Additionally, they must regularly test the quality of their components to determine if they meet all necessary industry guidelines. Quality control procedures should also be employed during every stage of manufacturing to minimize errors or defects in the final product. Not only does this help guarantee safety but it can also lead to increased efficiency and cost savings down the line.
Lastly, companies should always stay up-to-date on any changes that may occur within their sector so they can adjust accordingly and remain compliant with current regulations. By taking these steps throughout the production process, manufacturers can be confident that their laminated insulation material will not just meet but exceed industry standards.
Quality Control Measures for Laminated Insulation Materials
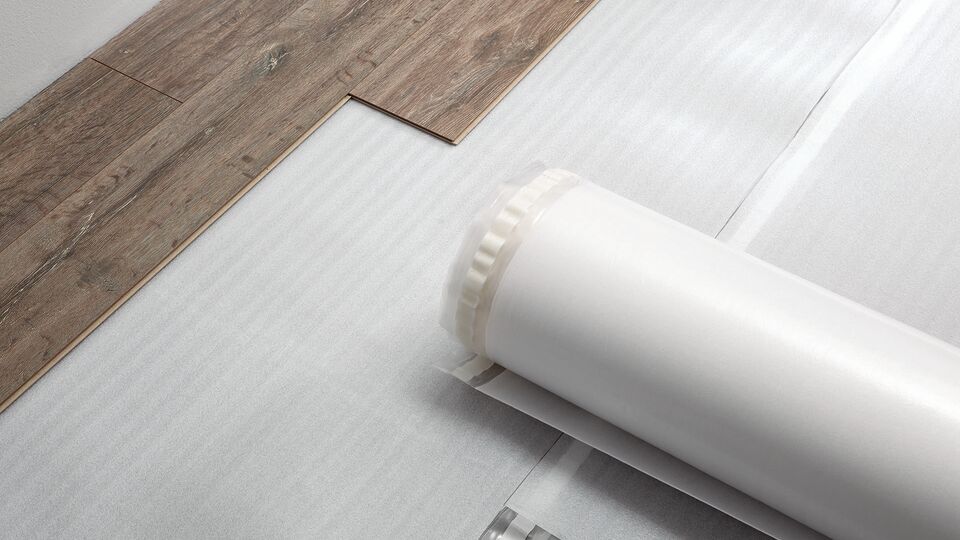
Quality control measures for the production of laminated insulation materials are essential to ensure that industry standards and regulations are met. To maintain a high level of quality, production processes must be monitored closely throughout each step.
This includes making sure all raw materials meet required specifications, verifying that all equipment is functioning properly, testing products periodically during production, and inspecting finished goods before shipment. In addition to these more traditional methods, advanced technologies such as computer vision and machine learning can be used to detect defects in real-time and alert operators when issues arise.
By utilizing these tools in combination with regular monitoring practices, manufacturers can help ensure their products exceed regulatory requirements while also providing customers with safe and reliable insulation solutions.
Compliance Procedures for Regulatory Bodies
Regulatory bodies have established compliance procedures that businesses must adhere to in order to produce laminated insulation material. These standards are set in place to ensure the safety and quality of the product and its performance, as well as its commitment to minimizing environmental impact. Companies must assess their production processes against these standards and regulations on an ongoing basis, making changes as necessary for compliance. Compliance is also required for proper labeling of any materials produced with hazardous components or chemicals.
A system should be implemented within each business that monitors all steps involved in producing the laminated insulation material, from sourcing raw materials to testing finished products before they are released into the market. Any non-compliance should be swiftly addressed and corrective action is taken if needed. Regular audits by regulatory bodies can help guarantee full adherence to all industry regulations which will ultimately protect consumers while ensuring a sustainable future for this important manufacturing sector.
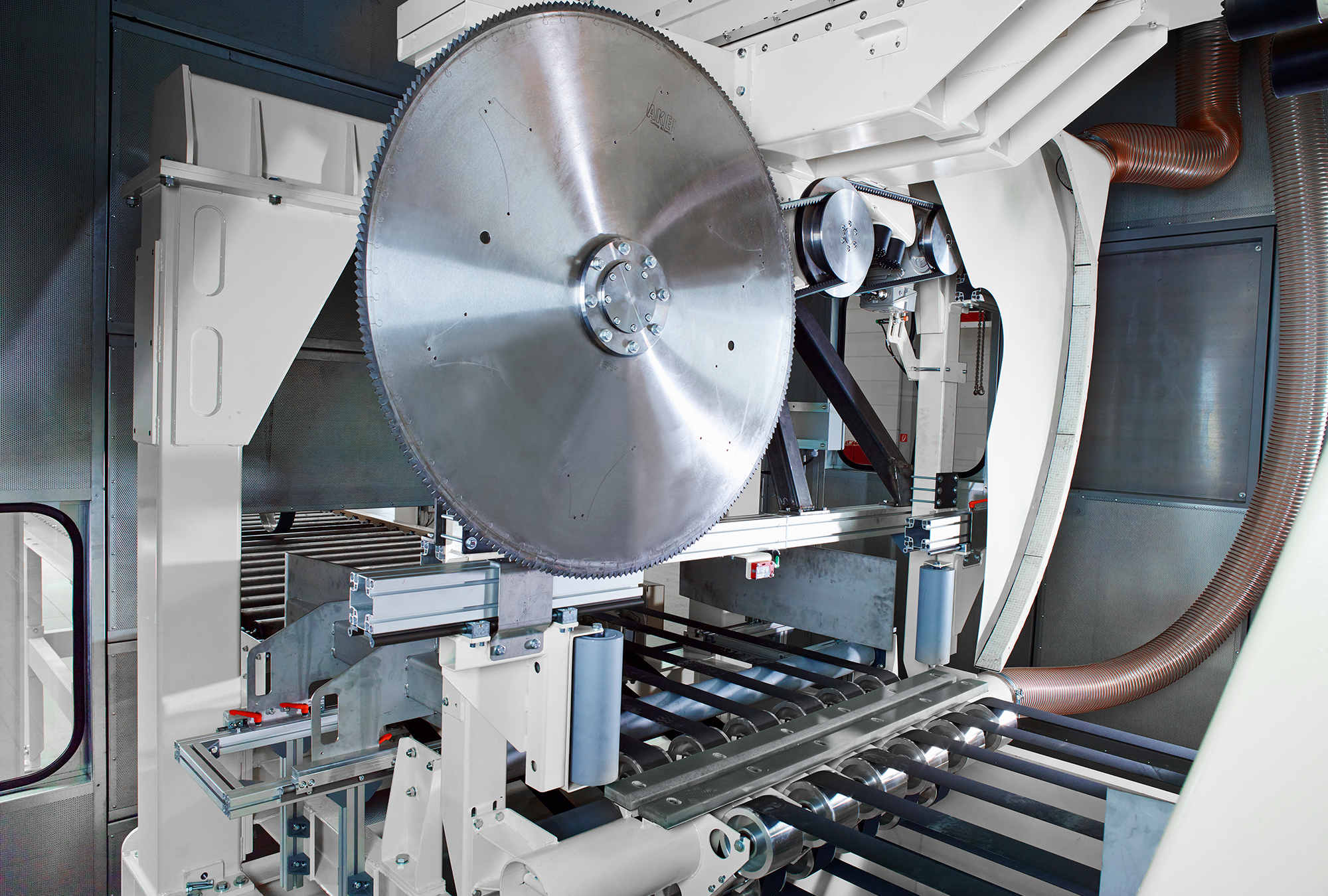